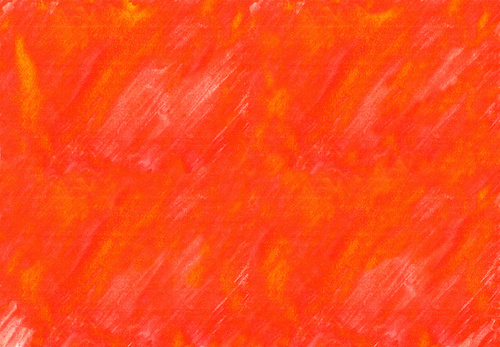
プラスチック製品の色ムラの原因
プラスチック製品の色ムラを発生させないためには、 どのようなプロセスで色ムラが発生するのか理解する必要があります。プラスチック製品の色ムラの原因には、大きく分けて3つの原因があり、それぞれで対策方法が異なります。
- 材料の攪拌不足
- 静電気が原因のこびりつき・張り付き
- 比重の違いによるムラの発生
材料の攪拌不足
ナチュラル色のプラスチック材料に着色するには、なんらかの着色剤を添加し着色する必要があります。目的の色に着色されたペレットを使用すれば、色ムラの発生や混合する手間もありませんが、価格が高く、現場での色味を調整することができません。そのため、現場では着色剤を使用して混ぜ合わせることが多くなっています。
着色剤を使用する方法では、ナチュラル色のプラスチック材料に着色剤を加え、混ぜ合わせる必要がありますが、このときの撹拌が足りないと色ムラが発生します。着色の方法は下記の3つが主流です。いずれの方法でも混合機などを使用し着色します。
- マスターバッチ:プラスチック材料に高濃度の着色剤が練り込まれたペレット状の着色剤。ナチュラルペレットとは比重が異なります。
- ドライカラー:粉末状の着色剤。安価ですが飛散しやすく、混合に時間がかかります。
- リキッドカラー:液体の着色剤。飛散はしませんが、混合に時間がかかります。
これらの方法では、着色剤の量によって色の濃淡を調整できますが、撹拌不足による色ムラが発生する危険性があります。上記のような方法で着色をしている場合は、撹拌不足をまず疑ってみるのがいいでしょう。
静電気が原因のこびりつき・張り付き
十分に撹拌した場合であっても、機械に着色剤がこびりつきや張り付きが発生し、色ムラの原因となる場合があります。このような問題は、静電気が原因で起こっている可能性があります。
先程紹介したマスターバッチペレットをナチュラルペレットに混合する際には、撹拌時に発生する摩擦でどうしても静電気が発生します。マスターバッチペレットとナチュラルペレットでは静電気を帯電する量が大きく異なるため、それが原因で混合機、ホッパーなどにひっつき、マスターバッチペレットの量が均一にならず、色ムラが発生する場合があるのです。
発生する静電気への対策としては、帯電防止剤が練り込まれた機能性マスターバッチペレットを使用するか、塗布型の帯電防止剤を利用するなどがあげられます。
色ムラの原因のほとんどは撹拌不足ですので、いきなり静電気での色ムラを疑うのではなく、撹拌不足がないか確かめた上で静電気による問題がないか確認してみるといいでしょう。
比重の違いによるばらつき
マスターバッチペレットを使用する場合、材料の輸送時に比重の違いで撹拌度合いに差が出る場合があります。マスターバッチペレットは、ナチュラルペレットに着色剤を高濃度で混ぜ込んだものです。そのため、ナチュラルペレットと比べると比重が重くなります。
材料を混合した後に、オートローダーのような機械でエアーなどを使用してホッパーに移動させると、材料比重の差によって輸送後にばらつきが生じる場合があります。この場合は、材料の輸送方法を変更するなどの工夫が必要になってきます。
色ムラが発生した場合にできる対策
樹脂成形で色ムラが発生した場合において、具体的にできる対策について紹介していきましょう。より簡単にできる順番で対策を紹介していきます。
- 撹拌時間を長くとる
- 背圧設定を高くする
- 加熱温度を高くする
- 帯電防止剤を使用する
- ミキシングノズルを使用する
撹拌時間を長くとる
色ムラの原因のほとんどが撹拌不足です。そのため、撹拌時間を長く取り、より着色剤とナチュラルペレットが混ざり合うように、撹拌時間を長く取るようにしてみるのが最も簡単で確実な対策です。まずはこちらの対策を試してみてください。
背圧設定を高くする
材料を射出する際に掛ける圧力を「背圧」と呼びます。この背圧を高めることで材料が混練されやすくなります。機械の設定だけで簡単にできる対策ですが、ノズル先端から材料が垂れる「ハナタレ」が発生する場合があります。その場合はサックバック値を高めるか、シャットアウトノズルを使用するなどの対策を行うといいでしょう。
加熱温度を高くする
加熱温度を上げることで、材料の流動性が高くなり混練性が高まります。ただし、温度を上げすぎるとガスの発生やバリの原因となってしまうため、その他の状態を見ながら調整していく必要があります。
帯電防止剤を使用する
マスターバッチペレットを使用している場合で、これまでの対策を施しても改善が見られない場合は、静電気の関係で色ムラが発生している可能性があります。このような場合は、帯電防止剤が練り込まれたマスターバッチペレットを使用するか、塗布タイプの帯電防止剤を添加するなどして対策すると効果的です。
ミキシングノズルを使用する
あらゆる対策を施しても色ムラが改善されない場合は、ミキシングノズルを使用し、成形直前の混練を高めるのが効果的です。 ミキシングノズルは比較的変更が容易な部品のため、導入はしやすいでしょう。ただし、射出する際の圧力が低くなる場合があるので、高圧での射出する製品にはあまり適しません。
<p style=”text-align: center;”><a class=”but1 bcolor1″ href=”https://form.k3r.jp/a_giken/arakawagiken”>加工のご相談はこちら</a></p>